Congratulations to Urban Valet Dry Cleaners on their new Morantz Ultrasonics B-136 “Baby” Blind Cleaner. Great day of training. Urban Valet is now ready to clean your mini blinds, vertical blinds, pleated shades, silhouette shades, wood blinds and more! — with Eric Pyne and Jackie O’Malley.
Author: Lisa Morantz
Thanks for 75 Great Years! Get your Anniversary Gift.
Thanks to all for making our 75th year of business a great success. Our last and BEST anniversary special still going on until December 31. Check out our new logo commemorating our long years of business history.
Morantz Ultrasonics at Interclean Exhibition
Morantz Ultrasonics journeys to Amsterdam bi-annually to participate in the world’s largest cleaning supply exhibition, Interclean. This year, up until the day we had planned to leave, we weren’t sure we were going to make it. The recent eruption of the Eyjafjallajokull Volcano in Iceland, that had shut down much of the air traffic across Europe, threated to prevent our trip and possibly, from the show taking place. Luckily there was a break in the ash cloud and we were able to take off without issue.
We had a great time meeting people in our industry from all over the world and showing them the myriad of benefits derived from Ultrasonic Cleaning. Here is a list of the countries we met people from: (Note: of course, the U.S.A. should be on this list too).
Even better, being at the tradeshow afforded us the opportunity to see many of our clients and to catch up with them. It’s always exciting for me to learn more about their businesses and how they are using their Ultrasonic Machines.
Amelia from Portugal let me know that she is using the machine primarily to clean parts for two major shipyards, and also for computer cleaning. She admitted that starting out 6 years ago trying to convince her clients to clean their computers with sound waves was not without its challenges. Now, she claims confidently, this is a niche market that is an in-demand service.
Sven from the Netherlands let us know that the blind cleaning machine he purchased from us 4 years ago paid for itself right away, and continues to be a revenue generator. While his company has cleaned many blinds in the machine, the entire staff came back to learn a bit more about how they can better market the ultrasonic cleaning service, and how they can diversify into other services such as contents restoration, parts cleaning and more.
We also were happy to see Adriana and her father, Gabriel, from the Canary Islands who have our SM-200 (Super Mighty One) system.
Neal and I, in an effort to not have to repack the M-115 (Mighty One) machine that we brought to the show, decided to put it up for sale. Sure enough, one of the fire restoration companies we had met two years previously at Interclean, purchased the machine. Below is the lucky new owner, Noel from Clean and Construct in Belgium. Before taking the machine back with him, he brought a few items to try out. Here you seem him pre-treating a greasy part that cleaned up beautifully.
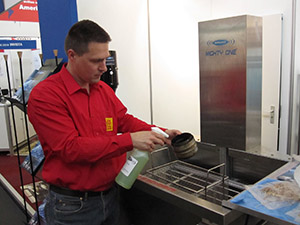
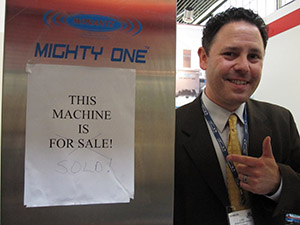
When not at the exhibition, we spent hours walking around, experiencing this vibrant city.
The beautiful architecture looks much the same as it did in the 1600’s.
On the last evening of the show, the city wide celebration of Queen’s Day began. It’s a national holiday in honor of the Queen’s birthday (although not the current Queen Beatrice, but her mother. The entire city became a sea of orange shirts, wigs, boas, balloons and more. I was told that Queen’s Day is the only day anyone can sell anything without a permit, so in essence the entire city is one big flea market. Maybe next time I’ll bring more machines to sell on the street at Queen’s Day (LOL!)
Overall, a great trip! We are looking forward to Interclean 2012.
Window Blind Cleaning on Social Media
For many of us, social media has become a standard in our lives. With the proliferation of Facebook, Twitter and other networks, I find myself on the internet more than ever discussing all types of topics with people from all over the world. But who would have ever thought that WINDOW BLIND CLEANING would have been one of those topics? Don’t take my word for it. Check out Facebook and Twitter where I found these messages:
“I hate cleaning wood blinds!!!, why did I have to get them everywhere in my house.”
“You could take em off & throw em in a tub…or buy a swiffer…I hate dusting blinds UGH!”
“Decided that cleaning window blind slats is right up there with silver polish; never gets done either.”
“Took down blind to clean it…took hours!”
“Cleaning a mini blind? Don’t bother. Its too hard.”
Recently I came across a Blog which threw out the simple question:
“What’s The Best and Easiest Way to Clean Blinds?”
Throughout the day, 21 people replied. Most people responded with their homemade bath tub type cleaning and dusting techniques. Interestingly, many of those people admitted that they were frustrated because the results of those methods were not that good. All this frustration leads to people absolutely hating the job of cleaning blinds!
Still not convinced? How about this response (you can really feel the frustration here):
“When asked how to clean; Yes there is a great way to take care of this problem! Make sure to read all the way through…even though this is easy, it is kind of detailed instructions. What you do: Mix a quart of vinegar, a small box of baking soda, in a bathtub about half to three quarters full of hot hot water. You need a hammer for this part. Take down all the horizontal mini-blinds in your home and hammer them to one inch pieces and set the pile on fire. Have the marshmellows handy! While your fire is getting the coals built up (because you can’t rush a great campfire) go online and order some vertical blinds, roman shades, or curtains for the windows in your home, all of which are easy to clean. Next, throw a beach towel over your naked bathroom window. Sprinkle some lavender oil or rose petals in the tub with the vinegar and soda water (which is great for the skin by the way) and celebrate your wise decision with a nice hot soak for your tired, stressed out, marshmellowy body. All this to say, I think mini-blinds are God’s way of mocking humans and I have NO idea how to deal with them. (WINK WINK HAHAHAHAHAHAHHHHHHAAAAAAAAAAAAA!)”
Despite all these posts, tweets, etc. The quote that follows is actually my FAVORITE response. It’s short and gets to the point:
“Pay to get them clean, that’s the easiest.”
And many, many people do pay to get their blinds cleaned.
The blog went on to discuss ultrasonic cleaning for blinds and stated:
“There are many benefits of ultrasonic cleaning such as they eliminate pollutants, germs, bacteria and move dust. And the best thing of this method is that you can clean your blinds at reasonable price. Another great advantage is that with the help of this method you can not only clean roller blinds but other types of blinds such as vertical blinds, office blinds, wooden blinds, mini blinds and Venetian blinds can be cleaned perfectly.“
At the end of the day, there’s an absolutely huge market that has proven itself time and time again to be profitable; and that market is cleaning window blinds with Ultrasonics.
Morantz Tradeshows Around The World
It’s been a very busy first quarter, complete with travel to The Cleaning Show in the United Kingdom, RIA tradeshow (Restoration Industry Association) in Palm Springs, California, Servpro of the Carolinas Conference in Charleston, South Carolina and Servpro of Penn Del Conference in Hershey, Pennsylvania. Throughout all of our travels, one thing has been clear…Ultrasonic Cleaning is now recognized, worldwide, as an extremely useful tool.
Here are a series of pictures from those shows.
Just this past weekend I had the privilege of speaking to Servpro franchises from Pennsylvania and Southern New Jersey.
While many of these franchises already own our equipment and have realized the benefits of high profit margins in content cleaning, others were seeing ultrasonics for the first time. I was happy to share with the group information about how the technology is not only applicable to fire restoration, but the diversification possibilities into medical cleaning, industrial parts cleaning, window blind cleaning, golf club cleaning and more. This aspect is very appealing to all types of business owners. Especially with the current economic recession, it is important to have a way to compensate for a revenue stream slow down by being able to easily pick up another.
One of our Servpro clients who purchased our Super Mighty One (SM-200) model and Drye Rite cabinet this past Summer, shared their story about their very first job with the ultrasonic machines. The job came from a flooded office building that had 54 computers and boxes full of telephones that needed cleaning (see pictures below).
It only took ONE employee (pictured below) to complete the entire cleaning job over the weekend!
She cleaned 3 computers at a time in the ultrasonic tank, and then placed them in the dryer until she filled the dryer (it fit 16 computers!). After 4 hours of dry time, she would remove the computers and fill the dryer with more newly cleaned computers.
Because of the quick turnaround, Servpro was able to walk back into the client’s office on Monday morning, set up the computers, and get them back to work. Now that’s service…and that’s ultrasonics.
A New Year
Happy New Year! I said this to a new client by the name of Jim who I spoke to on the phone this week. His reply was, “This is going to be the best year ever!!”
WOW! His response really resonated with me. Here is a guy that recently lost his job with a company he worked with for over 10 years. At a time when he has every right to feel confused, angry and even resentful, amidst the daily news reports of doom and gloom, he remains utterly and fantastically optimistic.
When I asked him how he could be so positive, he told me, “I have been waiting all my life to take control and not work for someone else. I was just too scared to do it before. Getting laid off was the best thing that could have happened to me because now I will set my own hours, be my own boss, and take control of my own destiny.”
…And he will. I have personally seen this scenario play out over and over again; people who have diligently worked for another boss for years finally having the opportunity to step out on their own and take charge. For many, it is a truly liberating and thrilling experience. They finally have the chance to live out their dreams and define what success means personally for themselves and their families. Although there is hard work involved with starting your own company, once things take off, our clients are then financially rewarded in ways that could never dream of as someone else’s employee.
Good luck Jim…I do believe you are right. This may just be the best year of your professional life.
Automotive Parts Cleaning with Ultrasonics
When it comes to cleaning Automotive Parts, the Ultrasonic process does an exceptionally good job. Whether it is grease, dust, rust, carbon, or other dirts, in most cases, these can be removed quickly and easily without hours of hand scrubbing or use of harsh chemicals.
I wanted to share with you some pictures from recent jobs that we’ve done.
Most recently, I had a client visit and he brought with him an intake manifold from a Ford Mustang engine. He was specifically looking for a way to clean parts prior to powder coating them. Here are the “before” pictures:
Here are photos of our client checking out the finished result:
Depending on the type of dirt we are dealing with, and the make up of the parts to be cleaned, we may work with either a 40kHz frequency (our standard) or a 25kHz frequency to get more aggressive. The rule of thumb is that the lower the frequency, the larger the bubble that is being produced and the more powerful the implosion in the Cavitation process. We also have 4 different cleaning solutions that we utilize depending again on the dirt and the part.
Take a look at the following before and after photographs of other automotive parts we have cleaned with Ultrasonics:
A few of the parts you see above are piston heads and exhaust lifters from a motorcycle. There are also rims from a Nascar race car. We have similarly cleaned helicopter parts, boat parts, airplane parts and more. Next week we will be trying something new…lawnmower parts…so check back soon.
Federal Express Uses Morantz Ultrasonics to Clean Ball Bearings
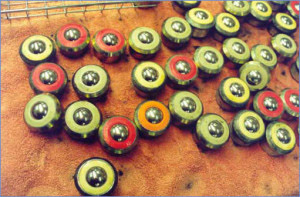
One of the things I love about my work is that I am constantly learning new things. On a regular basis, I am sent parts of all types from all over the world to either test clean or come up with a protocol for how they should be cleaned. Who knew that so many bars, valves, molds, nozzles, and other intricate objects were involved with creating so many others items? (OK…maybe you did, but this was not something I was exposed to until later in life).
So, I’ve come to learn a tremendous amount about parts in my past 15 years at Morantz, but it’s still surprising how primitive the attempt at maintenance is for many of these items. For example…
Several years ago, we were contacted by Federal Express. They wanted to know if we cleaned ball bearings. Specifically, they had ball bearings on their conveyor belts that were seizing up because of dirt, and sometimes de-icing chemical, that was getting into the crevices and preventing the balls from spinning. To rebuild the bearings, the cost was $30/each.
We did a trial cleaning and you could literally see the dirt streaming out of the small groove. When we gave Fed Ex a quote of $1.45 per bearing for cleaning, they were thrilled! The next thing we knew, we had 10,000 bearings at our facility to be cleaned (sent via Fed Ex, of course). Fortunately, our machines could easily accomodate 100 bearings at a time.
It only took about 10 minutes per load in our machines and we were able to complete the job in a day and a half. Again, Fed Ex was thrilled! In fact, when we returned the bearings to their distribution center, we were immediately given another 10,000 bearings! And this one facility had over 300,000 bearings that were contstantly being rotated in and out, and given to us for maintenance. Saying this was a great job is an understatement.
This was the beginning of a National contract that was ongoing throughout the country and utilized many of our clients. Everybody was a winner in this scenario.
Thanks, Fed Ex!
Cleaning Keyboards with Ultrasonics
Yesterday I was looking at my computer keyboard and realized that it was time to clean it. Like everyone else, I too sometimes eat at my desk, drop crumbs in the keyboard and have general dirt build up over time. Unlike everyone else, I have unlimited access to ultrasonic machines to clean my keyboard.
Before starting, I decided to take some photos so everyone could see this quick and easy process. I also took some readings both before and after the cleaning so that everyone could appreciate the cleanliness difference that ultrasonic cleaning really makes.
First, the Swab Test
We took a pre-swab for an ATP (Adenosine Triphosphate) test that measures bioluminesence or signs of bacterial life. This count gives a starting point and is a great way to verify that our cleaning is working. As you can see, the count on my keyboard was 181 (dirty!).
Most people don’t appreciate that their keyboards can be a breeding ground for germs. In fact, there has recently been much discovered and reported about in the news on how keyboards at nursing stations have been one of the main causes of the spread of MRSA in the hospitals both domestic and abroad.
Next, the Cleaning
Next, we submerged the keyboard for one minute in our M-115(Mighty One) ultrasonic cleaning system which is regularly used for cleaning electronics of all types.
Results
After removing the keyboard and drying it with both our Heated Blow Dry Gun and in our Drye Rite electronics drying station, we performed another ATP swab test. This time the result was only 29 which is great (for comparison, in the food industry, anything under 30 is considered to be excellent).
The result is that I am now typing this blog from a keyboard that looks better, functions better and is verified as clean. If you are currently working in or considering ultrasonic cleaning for offices, hospitals, schools and other public areas, I would recommend you consider ATP testing along with your ultrasonic process to show your clients the difference that ultrasonic cleaning makes.
New Clients Visit for Training
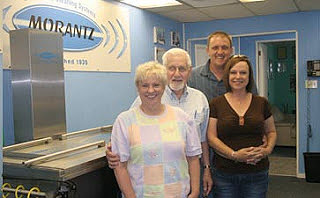
Today we welcome new clients to our family of Ultrasonic Cleaners. The team from Clean Blinds Now, David Morson, along with his fiancée, Cindy, his father Lamar and Lamar’s wife Hannah all completed 2 days of Basic Training at our Philadelphia headquarters and are headed back home to take delivery of their new 3-in-1 system.
Training is among my very favorite activities at Morantz Ultrasonics. While I do the majority of the teaching during training, I also make sure I spend time at the beginning of each session doing plenty of listening. This is my way of knowing what I really need to teach my clients to position them best for success. Believe me, it’s not the same for everyone. I’ve never approached our training as a set, static class. I individualize each training session for the needs of that client. This is the reason we conduct our basic training classes one on one and not in a group, classroom style.
For example, Dave and his family are a new, start-up business. They are planning to diversify into many different areas of ultrasonic cleaning including window blind cleaning, fire restoration and parts cleaning. To teach them everything they needed to know, I set aside two days. Beyond the basic know-how of the machine and cleaning techniques, we spent time talking about the family’s goals and expectations for the business. This helps me to make recommendations on things as diversified as marketing, pricing, and even the legal structure of the company (I am a lawyer, so I always ask about the nitty, gritty details to make sure everything is being thought through). However, if for example, I was training an existing fire restoration company, I would not approach the training the same way. Their needs are very different, as is each client’s needs.
I truly believe that training and support is the key to success in this business, and while each client has different needs, we are available for all of them. I told David before he left that he should feel free to call me and ask questions often….especially in the beginning when he is just getting started. He admitted that he is a bit anxious about everything but feels better knowing he can reach us should he need to.
Best wishes to the Morson family on their new venture!
Note: Shortly after this post, here is the note we received from the Morson’s:
Dear Stan, Lisa, Heather, and the entire Morantz Team.
We wanted to thank you for your hospitality, generosity, and wonderful experience we had coming to your operation. We look forward to embarking on a wonderful journey in the world of ultrasonic cleaning. The professionalism of each of your employees was unmatched. It was truly a pleasure dealing with each of them.
We are very excited to get started and look forward to many future dealings with your company.
Sincerely,
David, LaMar, and Hannah Morson
Clean Blinds Now